3.4 水輪機進水液控蝶閥技術規(guī)范 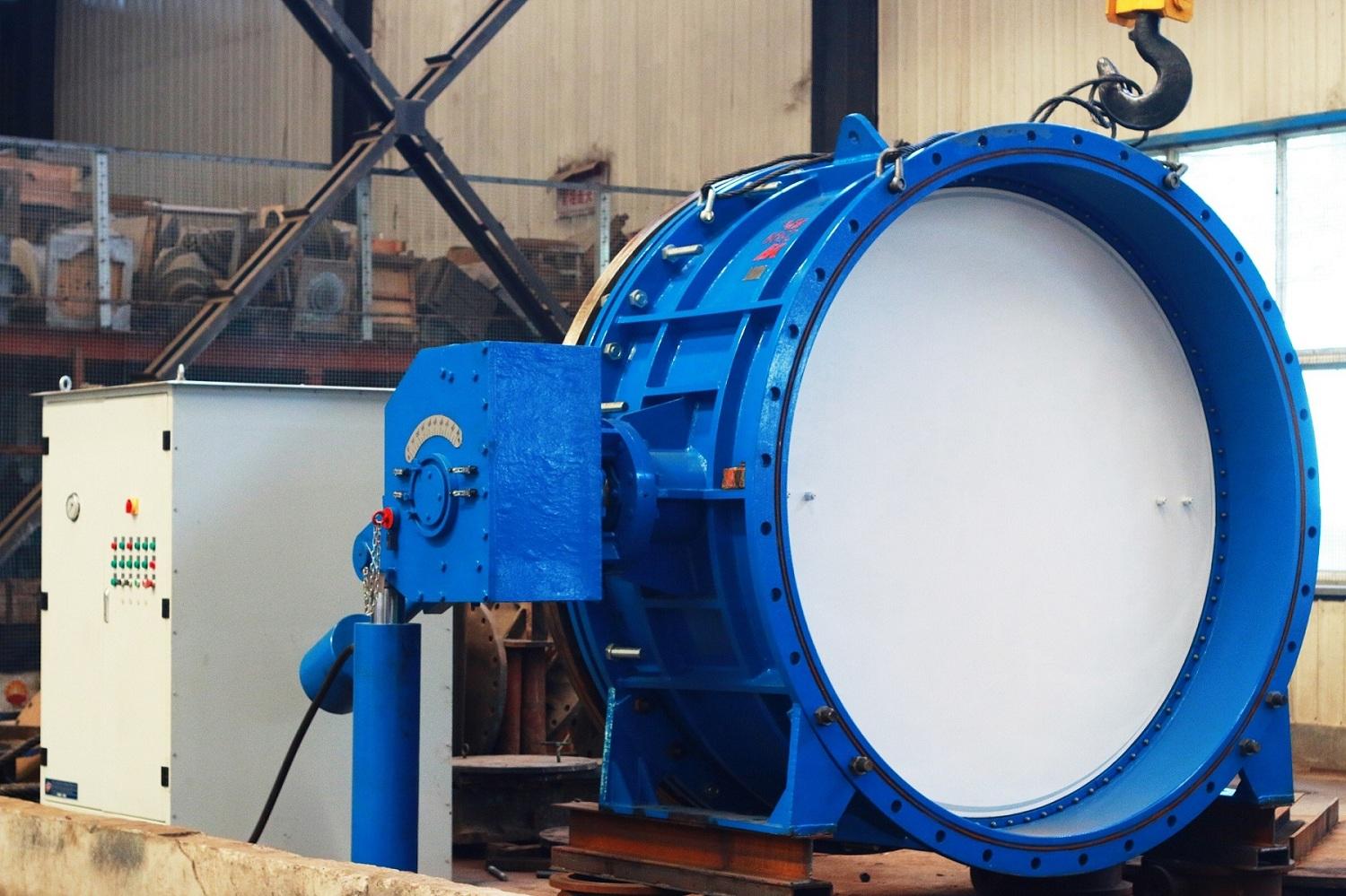
3.4.1 概述(1) 本條款是對本工程的2臺進水液控蝶閥及其附屬設備的模型試驗、設計、制造、工廠組裝和試驗、設備交貨作出技術規(guī)定。 (2) 進水液控蝶閥及其附屬設備應用的材料、材料試驗、工作應力、工藝、焊接、檢驗和其他一般技術要求可以滿足本條款的規(guī)定。 (3) 進水液控蝶閥及其附屬設備包括: 進水閥、操作機構(液壓操作)、伸縮節(jié)、湊合節(jié)、旁通閥、檢修閥、旁通管路、空氣閥、排污閥、控制柜、自動化元件、設備之間的連接管路、附件、控制電纜、基礎螺栓、上下游側(cè)法蘭聯(lián)接所需的全部螺栓、螺帽、填料、墊圈、墊板以及裝拆和維護的專用工器具、備品備件等。 (4) 標準及規(guī)范 下列標準及規(guī)范是賣方必需遵守的: DL/T 507-2014 | 水輪發(fā)電機組啟動試驗規(guī)程 | GB/T 14478-2012 | 大中型水輪機進水閥門基本技術條件 | GB/T 13927-2008 | 工業(yè)閥門 壓力試驗 | GB 150-2011 | 壓力容器 | GB/T 11805-2019 | 水輪發(fā)電機組自動化元件(裝置)及其系統(tǒng)基本技術條件 |
賣方在設備設計、制造、安裝中應在上述標準中,優(yōu)先采用中華人民共和國國家標準,在國內(nèi)標準缺項或不完善時,可參考選用相應的國際標準或其它國家標準。 (5) 賣方提供的圖紙和資料 1) 賣方在訂貨合同生效后的45天內(nèi),向江西省水利規(guī)劃設計研究院提供下表中的圖紙。這些圖紙應比投標文件的圖紙更完善,包含了在簽訂合同過程中已澄清的內(nèi)容,并作為設計聯(lián)絡會議的基本文件。 2) 賣方依據(jù)合同的規(guī)定,向買方提供圖紙資料。但買方或江西省水利規(guī)劃設計研究院對圖紙資料的認可,并不免除賣方的技術責任。 3) 本條款所列圖紙和資料目錄是賣方至少應提交的,并不代表是全部。買方視情況有權提出所需的其他圖紙和資料,賣方不得拒絕。 賣方正式提交審查的資料均應由賣方授權代表簽署和單位蓋章。所有資料上應標明“江西省鷹潭市花橋水利樞紐工程施工圖專用”字樣。 賣方需提交的技術文件 序號 | 圖紙及資料名稱 | 交付時間(天) | 備注 | 1 | 電氣原理圖 | 45 |
| 2 | 電氣接線圖 | 45 |
| 3 | 機械液壓系統(tǒng)圖 | 45 |
| 4 | 液控蝶閥(含液壓站)總裝圖 | 45 |
| 5 | 液控蝶閥(含液壓站)基礎受力圖 | 45 |
| 6 | 液控蝶閥流阻曲線圖 | 45 |
| 7 | 安裝、使用、維護說明書 | 45 |
| 8 | 液控蝶閥、自動化元件交貨明細表及裝箱單 | 45 |
| 9 | 其它圖紙 | 45 |
|
3.4.2 承包范圍進水蝶閥的承包范圍為2臺套水輪機進水液控蝶閥及其附屬設備的供貨和相應的備品備件、專用工具、技術資料以及有關的技術服務等。 招標范圍包括上述設備的設計、制造、出廠前試驗、包裝、運輸至工地買方指定地點、參加現(xiàn)場開箱檢查;提供安裝、調(diào)試指導和技術培訓;參與現(xiàn)場試驗、特性試驗、試運行和驗收;產(chǎn)品技術文件編制和提交等。 進水蝶閥包括以下內(nèi)容: 1) 2套水輪機進水液控蝶閥及其操作機構,基礎裝置與基礎螺栓,連接所需的全部螺栓、螺帽、填料、墊圈、墊板等。 2) 2套鋼制伸縮節(jié)。 3) 2套上、下游連接管及其連接件等。 4) 2套進水閥液壓站、操作油管路系統(tǒng)、電液控制設備(含控制柜)、電纜等。 5) 2套進水閥用的旁通閥、檢修閥及其附件。 6) 2套控制與監(jiān)測用自動化元件。 7) 1套專用工器具和備品備件。 3.4.3 型式和主要參數(shù) 型式: 臥軸雙平板液動蝶閥; 閥軸的布置方式: 臥式; 操作機構型式和操作方式: 接力器型式和油壓操作; 閥門公稱直徑: DN1400~DN1500(具體在設聯(lián)會上定); 公稱壓力: 0.6MPa; 伸縮節(jié)公稱直徑: 同蝶閥; 旁通閥直徑: ≥DN150; 空氣閥直徑: ≥DN150; 液壓系統(tǒng)工作壓力: 16MPa; 閥門的開啟時間: 60s~120s(可調(diào)); 閥門的關閉時間: 60s~120s(可調(diào)); 進水閥裝置控制方式:中控室遠控和現(xiàn)場操作兩種方式。 3.4.4 技術要求和運行條件(1) 進水閥及其附件的設計工作壓力為0.6MPa。 (2) 進水閥的額定過流量約5.59m3/s。正常情況下,進水閥在機組導葉全關狀態(tài)下開關,非常情況下,進水閥可在機組導葉全開度開啟時動水關閉。 (3) 機組正常停機或檢修時進水閥應能可靠而嚴密的關閉。關閉應靈活、平穩(wěn)、準確。 (4) 進水閥開啟前,應開啟旁通閥向閥后充水平壓,當閥兩側(cè)的壓力差不大于30%的最大靜水壓力時,進水閥應能靈活、平穩(wěn)、準確的開啟。 (5) 在機組任何運行工況下(含機組處于最大飛逸工況),進水閥應能在120s(可調(diào))內(nèi)動水關閉,關閉時應無有害的振動。 (6) 進水閥的活門只處于全開或全關位置,不作調(diào)節(jié)流量用。 (7) 進水閥應有足夠的強度和剛度,能承受任何工況下可能產(chǎn)生的最大水壓及水壓試驗而不產(chǎn)生破壞及有害變形。上下游法蘭應能傳遞出現(xiàn)的最大軸向力,閥殼配有堅固的底座能把全部垂直荷載包括延伸部件和水的重量、接力器拉力等安全地傳遞到混凝土基礎上。 (8) 進水閥底座應容許鋼管的少量伸縮帶來的位移,底座底面與底板接觸面要加工光滑。 (9) 進水閥應能手動和自動操作,可在現(xiàn)地和遠方監(jiān)控。 (10)進水蝶閥全開時的水流阻力系數(shù)應小于0.15。 (11)進水蝶閥在電站最大靜水頭下,持續(xù)30min允許的最大漏水量Q≤0.16L/min。 (12)進水閥應具有下列可靠性指標: 大修間隔期不少于10年; 退役前使用壽命不少于40年; 開關次數(shù)不少于10000次。 無故障連續(xù)運行時間18000h 可利用率99.6% 3.4.5 進水閥結(jié)構和材料3.4.5.1 閥體 (1) 閥體采用鑄鋼或鋼板焊接結(jié)構制造,上下游用法蘭連接。為使閥體具有足夠的強度和剛度,在閥體外側(cè)設有雙肋板復式加強筋,保證在最不利工況下將閥體的變形控制在允許范圍內(nèi)。任何點的最大工作應力不能超出本卷的規(guī)定。 (2) 閥體上軸承座為箱式結(jié)構,軸承箱采用材質(zhì)不低于ZG25的鑄鋼件經(jīng)初加工后與閥體焊接在一起。軸承箱應能承受在最不利工況下閥軸傳來的集中荷載。 (3) 主密封設在閥體下游側(cè),利用活門關閉時承受的水壓壓緊實心橡膠密封圈,以提高閥門的密封性能。閥體上密封面采用材質(zhì)不低于1Cr18Ni9Ti不銹鋼層,保證在任何情況下不發(fā)生銹蝕。 (4) 閥體過水面應進行機加工,并滿足有關規(guī)范對表面粗糙度的規(guī)定。 3.4.5.2 活門與閥軸 (1) 活門用鑄鋼或鋼板焊接制造,活門與閥軸采用螺栓連接。活門過流表面的形狀應具有良好的水力特性,過流表面應加工并滿足本卷對表面粗糙度的規(guī)定,以減小水頭損失和水力振動。 (2) 活門應采用偏心結(jié)構,具有必要的水力自關閉性能。 (3) 活門采用雙平板板桁架結(jié)構,其構件應受力合理,并通過有限元分析計算,使最大工作應力控制在本卷規(guī)定范圍內(nèi),以保證結(jié)構強度和可靠性。 (4) 活門密封采用優(yōu)質(zhì)高硬度實心橡膠圈,整體硫化,無縫連接方式,用不銹鋼壓板和螺釘固定在活門上。閥門所需密封比壓通過螺釘調(diào)節(jié),并可在不拆卸閥體的情況下,檢修和更換密封圈。 (5) 閥軸采用鍛鋼制造,閥軸與軸承及軸頸密封接觸的部位堆焊不銹鋼,加工后不銹鋼厚度不小于5mm。活門與閥軸的連接采用螺栓預緊力及橫銷傳遞扭矩的連接方式。 (6) 閥軸密封應具有自補償功能,并有有效的防泥沙進入的措施,密封材料采用具有高彈性、耐磨、成形好、自潤滑性好的復合材料或聚乙烯材料。可在不拆開閥殼的情況下更換活門軸頸密封。 (7) 在閥軸鋼套或轉(zhuǎn)臂上設有活門全開和全關位置信號器(開關量信號)。 3.4.5.3 軸承 (1) 軸承由軸瓦、鋼套、橡膠密封圈和壓墊環(huán)、軸承箱等組成。 (2) 軸承采用鋼背復合材料制造,應具有自潤滑性能,不需外加潤滑油脂。 (3) 軸瓦內(nèi)外側(cè)兩端和鋼套外壁兩端應設有密封圈。 3.4.5.4 操作機構 (1)進水閥操作機構由接力器、轉(zhuǎn)臂、鎖錠裝置、管路、節(jié)流閥和附件等組成。 (2)接力器為直缸雙向運行搖擺式,采用油壓操作,布置在進水閥一側(cè)或兩側(cè),支撐在閥室底板上。 (3)為避免進水閥在動水關閉過程中引起振動,在接力器液壓系統(tǒng)中應裝設可調(diào)式節(jié)流閥。 (4)進水閥活門全關位置應設有可靠的鎖錠裝置。鎖錠裝置分為液壓式和機械式,液壓鎖錠裝置設有鎖錠投入和退出的狀態(tài)信號,除在現(xiàn)地顯示外,應輸出至少一對狀態(tài)信號接點。鎖錠裝置的投入、拔出應有現(xiàn)地和遠方控制,可由進水閥操作程序控制。鎖錠的動作必須準確、可靠,鎖錠未拔出,進水閥不能操作。 (5)機械鎖錠裝置必須有足夠的強度,能承受接力器的最大操作力。機械鎖錠裝置在進水閥全關后手動投入,保證閥后設備檢修時安全可靠。機械鎖錠裝置設有鎖錠投入和退出的狀態(tài)信號。 (6)操作機構應能保證在電站機組任何工況下和事故時動水關閉進水閥,保證閥后設備的安全。 3.4.6 進水閥附件3.4.6.1 概述 進水閥附件指伸縮節(jié)、上游連接管、下游連接管、旁通管路與閥門、檢修閥等。 3.4.6.2 伸縮節(jié) (1) 伸縮節(jié)為鋼制套筒式、免維護、零泄漏型,伸縮節(jié)裝設在進水閥下游側(cè),公稱直徑同蝶閥,設計壓力為0.6MPa,伸縮量為10~20mm。 (2) 伸縮節(jié)與壓力鋼管采用焊接,與進水閥下游側(cè)采用法蘭連接。進水閥伸縮節(jié)應拆裝方便,并應有可靠的密封裝置,在電站安裝后伸縮節(jié)不得漏水。伸縮節(jié)不應對水輪機進水管道和進水閥產(chǎn)生任何有害的軸向作用力。 (3)伸縮節(jié)下游側(cè)直接與蝸殼進口變徑管法蘭連接。 3.4.6.3 上游連接管 在進水閥上游側(cè)設置長約1.0m、直徑與進水閥相同的連接管,一端與閥體法蘭連接,一端與電站壓力鋼管焊接連接,具體長度以滿足現(xiàn)場實際需要為準。上游連接管公稱壓力0.6MPa,鋼管厚度及材質(zhì)應與壓力鋼管相匹配,不需預熱即能在現(xiàn)場與其連接的壓力鋼管進行焊接。連接管流道上部應設置壓力傳感器和旁通管接口。 3.4.6.4 旁通管路 (1) 進水閥應設置一路直徑不小于DN150的旁通管路,布置在進水閥上側(cè)部。 (2) 旁通閥采用電動偏心半球閥。 (3) 若旁通管路跨過進水閥后的伸縮節(jié),則旁通管路也應設置伸縮節(jié)。旁通閥前設有檢修閥。檢修閥為偏心半球閥,渦輪傳動、手動操作。 (4) 在進水閥閥殼應設支撐,支撐旁通管路。 3.4.7 進水閥控制系統(tǒng)進水閥控制系統(tǒng)由液壓站和控制系統(tǒng)二部分組成。其基本原理是:液壓站通過油泵機組向蓄能罐充油而產(chǎn)生壓縮能或存貯液壓能,在電控指令和控制閥組的作用下,蓄能罐的液壓油經(jīng)液壓閥快速流向操作機構,而將液壓能轉(zhuǎn)變?yōu)闄C械能,從而在驅(qū)動主接力器、鎖定接力器等過程中實現(xiàn)進水閥的動作功能。 3.4.7.1 液壓站(機械液壓系統(tǒng)) 進水閥的壓力油源的額定油壓不低于10MPa,事故低油壓為額定油壓的60%,操作油號為:L-TSA-46(GB11120)。 液壓站由油泵組、蓄能罐、回油箱、管路、閥門、表計、壓力繼電器、液位指示器、液位信號器、濾油網(wǎng)和附件等組成。 (1)油泵組 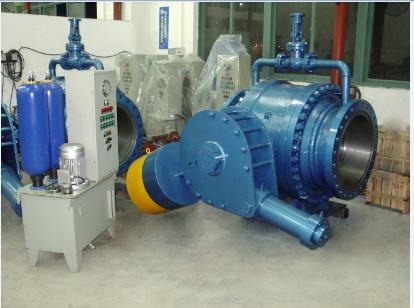
1) 液壓站應有2臺相同的電動油泵,一臺工作、一臺備用,且互為主備用。每臺電動油泵每分鐘的供油量不應小于接力器總有效容積的0.65倍,電動油泵由低起動電流的三相感應電動機直接驅(qū)動,并可連續(xù)工作,電機絕緣等級為F,且具有良好的防潮性能。 2) 每臺油泵應配有卸荷閥、安全閥、截止閥、止回閥。 3) 油泵應既能單獨運行又能聯(lián)合運行,在聯(lián)合運行時,油泵應能自動交替作主用泵,同時也能手動選定主用泵。當油壓降低時啟動主用泵,當油壓力繼續(xù)下降時自動啟動備用泵并發(fā)信號,油壓恢復正常值時自動停止工作泵和備用泵。為滿足控制要求,應配置足夠數(shù)量的壓力繼電器。 4) 另配設一臺手動油泵作為調(diào)試和檢修備用,手動油泵的排油能在10min內(nèi)開、關進水閥。 (2)蓄能罐 1) 蓄能罐的總?cè)莘e應不少于4.5倍進水閥接力器的總?cè)莘e,同時還應滿足進水閥關-開-關三次動作,其中最后一次關閉不啟動油泵,壓力油罐尚存必須的油量和保持最低允許油壓的要求。 2) 蓄能罐的設計、制造、試驗、驗收和證明均應按照ASME標準《鍋爐和壓力容器規(guī)程》第Ⅷ章第1部份的標準或GB150進行,最大允許工作壓力應不小于系統(tǒng)最大運行壓力的1.2倍。 3) 蓄能罐應配有壓力表、壓力信號器、帶有閥門的整套油位指示計、油位信號器、安全閥、供氣接口、充氣裝置,壓力信號器和油位信號器在油壓和油位變化時,能可靠地發(fā)出信號,自動保持油壓和油位都在設計范圍內(nèi)。 每只蓄能罐的底部還應裝設排油管和排油閥。 (3)回油箱 1) 回油箱的容積應能容納進水閥操作系統(tǒng)全部油量的1.2倍。 2) 回油箱內(nèi)回油區(qū)和凈油區(qū)間應設有濾網(wǎng),濾網(wǎng)應便于更換和檢修。回油箱應設油位指示器、油位信號器、加油口接頭和閥門、化驗取油樣閥門以及循環(huán)濾油用的接頭和閥門。 3) 回油箱應無裂紋、裂縫或盲孔,所有焊縫要連續(xù),并經(jīng)熱油滲透試驗合格,回油箱內(nèi)表面涂刷耐油漆,其外面涂刷防銹漆和面漆。 (4)管路與閥門 1) 機械液壓系統(tǒng)包括液壓站、控制柜、接力器之間的管路、閥門和管件。 2) 管路采用無縫鋼管和高壓軟管,剛性管路采用法蘭連接,與柔性管采用卡套連接,管路系統(tǒng)的公稱壓力應滿足液壓系統(tǒng)最大運行壓力的要求。 3) 整個管路系統(tǒng)的密封應嚴密,保證不漏油。 3.4.7.2 電氣控制系統(tǒng) (1) 進水閥及其附屬設備采用PLC控制,應能在現(xiàn)地和遠方按規(guī)定程序自動或手動操作,設備的動作應準確、可靠。PLC應采用國際知名品牌,為工業(yè)級產(chǎn)品。 (2) 進水閥的開、關程序與機組操作程序相適應,接受機組操作程序發(fā)出的開、關閥命令,并按設計程序程序執(zhí)行,應能以一個命令脈沖完成從全關—(開啟旁通閥)充水平壓—拔出鎖錠—全開—關閉旁通閥;或者全開—全關—投入鎖錠的過程。 (3) 進水閥的PLC控制系統(tǒng)能實現(xiàn)與電站計算機監(jiān)控系統(tǒng)的通信,其串行通訊接口宜采用RS485接口,最終方案在設計審查會上確定。 機組操作程序發(fā)出的開關閥命令,除了可以通過RS485串口與進水閥PLC通信以外,還需要有開關量硬接點并行聯(lián)通。 (4) 進水閥控制電源采用直流220V。 (5) 進水閥可在下述情況下開啟 1) 在機組正常開機程序中自動開啟; 2)根據(jù)需要可遠方或現(xiàn)地手動控制開啟。 (6) 進水閥可在下述情況下關閉 1) 在調(diào)速系統(tǒng)失靈,機組過速超過最大速率上升值5%和主配壓閥拒動機組過速115%,進水閥自動動水關閉; 2) 當進水閥和導葉之間的壓力水管、伸縮節(jié)、蝸殼破裂或排水閥、取水閥爆破或故障時,可根據(jù)需要手動緊急動水關閉; 3) 在機組正常停機程序中可根據(jù)監(jiān)控指令自動停機聯(lián)動關閉; 4) 根據(jù)需要可遠方或現(xiàn)地手動控制關閉。 (7) 進水閥液壓操作系統(tǒng)的壓力降至事故低壓力時,應立即發(fā)出報警信號,而不應自動關閉。 (8) 進水閥的開啟所需的差壓信號由裝設在上、下游連接管上的壓力傳感器提供。 (9) 進水閥開、關完畢后,應自動關閉接力器壓力油總管,撤消接力器的油壓,依靠鎖錠或其他可靠的措施保持活門在全開或全關位置和必要的密封壓力。 (10) 進水閥及其附屬設備的開啟、關閉順序由賣方提供,經(jīng)買方工程師審查同意后確定,其電氣回路的程序編制、動作正確性等由賣方負責。 (11) 進水閥設置控制柜。控制柜內(nèi)裝設電磁操作閥、液壓操作閥、儀表、自動化元件、指示燈、手動按鈕、電氣端子、管路、閥門和電加熱器等。 (12) 進水閥設有行程指示器和行程傳感器,并有全開和全關位置的開關接點輸出。 (13) 進水閥控制柜上應有下列信號、顯示、輸出接點以及儀表,帶*者還要求輸出模擬量DC4~20mA,將引至計算機監(jiān)控系統(tǒng): 1) 進水閥全開、全關的位置信號; 2) 進水閥鎖錠投入與拔出的信號; 3) *進水閥上下游壓力差的差壓信號; 4) 旁通閥開關位置信號; 5) *蓄能罐內(nèi)油壓過高、過低和事故低油壓的報警信號; 6) 進水閥上、下游壓力; 7) 進水閥操作油壓; 8) 油泵交流電源消失故障信號; 9) *進水閥直流控制電源消失故障信號; 10) *備用油泵啟動信號; 3.4.8 工廠組裝和試驗3.4.8.1 設備發(fā)貨前應在廠內(nèi)對進水閥、旁通閥、旁通管及伸縮節(jié)等進行組裝,并對各主要尺寸和裝配尺寸進行檢驗,必要時加定位銷和裝配記號。 3.4.8.2 進水閥及其附屬設備承受水壓、油壓、氣壓的部分,除需在工地進行焊接的部分外,均需在廠內(nèi)參照“大中型水輪機進水閥門基本技術條件”進行水壓試驗。 3.4.8.3 進水閥活門的水密封焊縫應作磁粉探傷或著色探傷試驗,保證水密。 3.4.8.4 進水閥在制造廠內(nèi)總裝后進行漏水試驗,試驗壓力為電站最大靜水壓力25.9m水柱,進水閥漏水量應滿足性能保證值。漏水試驗時,閥門的軸頸密封不允許漏水。 3.4.8.5 旁通閥應在0.6MPa壓力下進行水壓試驗,不允許滲漏。 3.4.8.6 伸縮節(jié)應在0.6MPa壓力下進行水壓試驗,不得滲漏。 3.4.8.7 進水閥及其附屬設備工廠組裝和試驗項目見表3.4.8-1。 3.4.8.8 賣方應及時將廠內(nèi)試驗報告、測量記錄、材質(zhì)合格證明等資料提供給買方監(jiān)理工程師審查,審查合格簽字后設備方可出廠。
|